firstgear
Well-known member
- Joined
- Oct 11, 2003
- Messages
- 1,895
- Location
- Norwalk, Ohio
- Corvette
- 15 Z06, 01 Vert, 63 SWC & 60 ALL RED
One of the guys I work with is a big boat and airplane nut and talked me into using the WEST system of 2 part epoxy along with fiberglass or carbon fiber, depenidng on the gap to be filled.
In the case of the '63 the rear wheel wells were moved inboard about 5.5 inches. I bought some black carbon fiber in 6 inch and 4 inch tape (meaning that the sides are closed and it won't fray all over) I also bought some WEST 105 epoxy resin, 205 epoxy hardner and 404 high density filler.
WEST also sells the pumps that go into the container bung holes. Those pumps are sized to give you the exact ratio you need. One push on each pump, then mix them up will give the percise ratio needed.
Black carbon fiber tape, 4" and 6"
Regular fiberglass tape, 4" and 6"
This is the kind of gap that I had to bridge
Cardboard with wax paper on top of it was used to make a backer and then it was held in place with lots of duct tape. I needed to make sure that the carboard was up tight against the fiberglass otherwise I would end up leaking out the epoxy (which did happen in a few places).
The nice part about the epoxy is that it has a lot of open time. Anywhere from 1/2 hour to an hour before it really starts to get tacky. I bought some cheap paint brushes on EBay, since when you are done, you pitch them.
Jeff and I painted the epoxy mixture onto the wax paper and then up on the sides of the rear wheel wells. We laid the 6" wide piece of carbon fiber into the gap and made sure that it was rolled nicely into the seams as well as the edges. Then another application of epoxy mixture with the paint brush and this time we took two 4 inch pieces and overlapped them in the center as well as onto the outside edges, again making sure that we had enough wet out by using the roller.
Finally we took the epoxy mixture and brushed it all over the carbon fiber. In about 18 hours it is dry to the touch and fully cured in about 24 hours depending on the tempreature your garage is at. West quotes everything at 70 degrees F with a minimum application temperature of 40 degrees F.
Since boat hulls have lots of vertical surfaces, they sell an additive called 404 High Density Filler, a kind of powder filler that you mix in to the epoxy mixture.
They suggest a couple of different thicknesses that you can achieve by the amount of filler you add. From "catsup" to "mayonnaise" to "peanut butter" consistencies.
And here is the final bridging with black carbon fiber. The rest of the rear wheel well might fall apart, but the black carbon fiber will be there for a long time.
I used regular fiberglass tape on the butt joint just to the inside of the wheel well. I have a large piece of fiberglass board that will cover the flat are completely butting up the the metal reinforcement that will rise up right behind the seats (in front of the old storage area comparment now gone).
I will add another layer of 6" wide glass down the middle of the wheel wells to help build that area up prior to skin coating. After fussing with this, I really appreciate those that have had to do entire cars or made a Gran Sports as I can imagine the amount of glass work/fussing that they had to do.
In the case of the '63 the rear wheel wells were moved inboard about 5.5 inches. I bought some black carbon fiber in 6 inch and 4 inch tape (meaning that the sides are closed and it won't fray all over) I also bought some WEST 105 epoxy resin, 205 epoxy hardner and 404 high density filler.
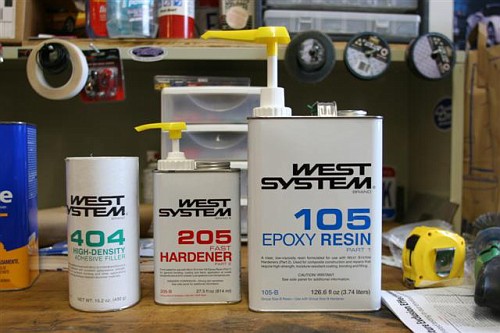
WEST also sells the pumps that go into the container bung holes. Those pumps are sized to give you the exact ratio you need. One push on each pump, then mix them up will give the percise ratio needed.
Black carbon fiber tape, 4" and 6"
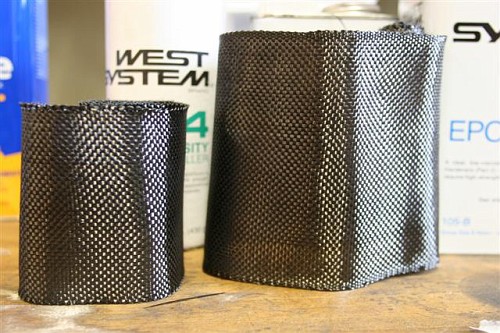
Regular fiberglass tape, 4" and 6"
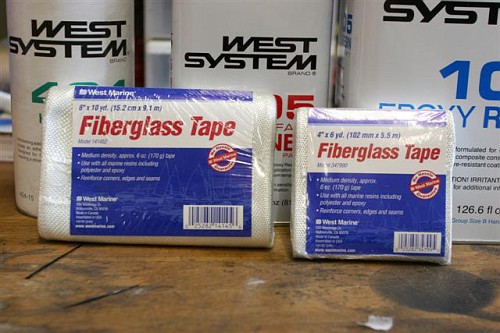
This is the kind of gap that I had to bridge
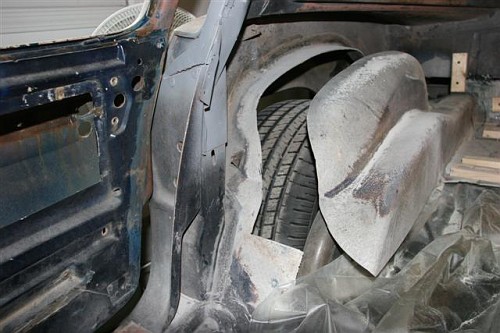
Cardboard with wax paper on top of it was used to make a backer and then it was held in place with lots of duct tape. I needed to make sure that the carboard was up tight against the fiberglass otherwise I would end up leaking out the epoxy (which did happen in a few places).
The nice part about the epoxy is that it has a lot of open time. Anywhere from 1/2 hour to an hour before it really starts to get tacky. I bought some cheap paint brushes on EBay, since when you are done, you pitch them.
Jeff and I painted the epoxy mixture onto the wax paper and then up on the sides of the rear wheel wells. We laid the 6" wide piece of carbon fiber into the gap and made sure that it was rolled nicely into the seams as well as the edges. Then another application of epoxy mixture with the paint brush and this time we took two 4 inch pieces and overlapped them in the center as well as onto the outside edges, again making sure that we had enough wet out by using the roller.
Finally we took the epoxy mixture and brushed it all over the carbon fiber. In about 18 hours it is dry to the touch and fully cured in about 24 hours depending on the tempreature your garage is at. West quotes everything at 70 degrees F with a minimum application temperature of 40 degrees F.
Since boat hulls have lots of vertical surfaces, they sell an additive called 404 High Density Filler, a kind of powder filler that you mix in to the epoxy mixture.
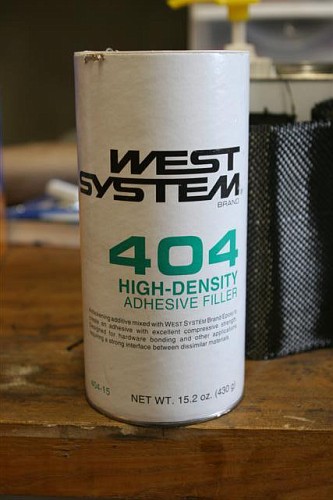
They suggest a couple of different thicknesses that you can achieve by the amount of filler you add. From "catsup" to "mayonnaise" to "peanut butter" consistencies.
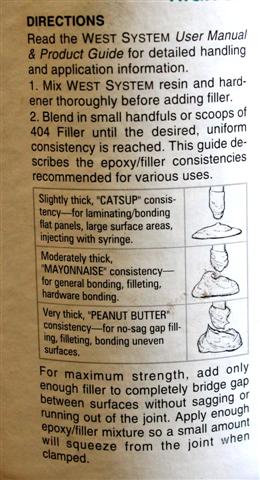
And here is the final bridging with black carbon fiber. The rest of the rear wheel well might fall apart, but the black carbon fiber will be there for a long time.
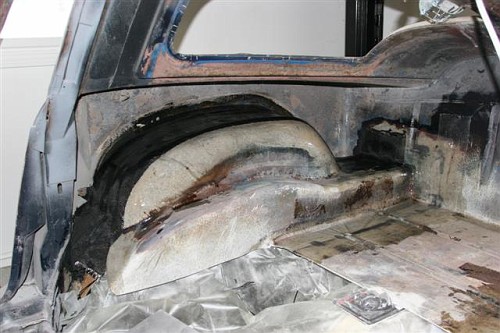
I used regular fiberglass tape on the butt joint just to the inside of the wheel well. I have a large piece of fiberglass board that will cover the flat are completely butting up the the metal reinforcement that will rise up right behind the seats (in front of the old storage area comparment now gone).
I will add another layer of 6" wide glass down the middle of the wheel wells to help build that area up prior to skin coating. After fussing with this, I really appreciate those that have had to do entire cars or made a Gran Sports as I can imagine the amount of glass work/fussing that they had to do.
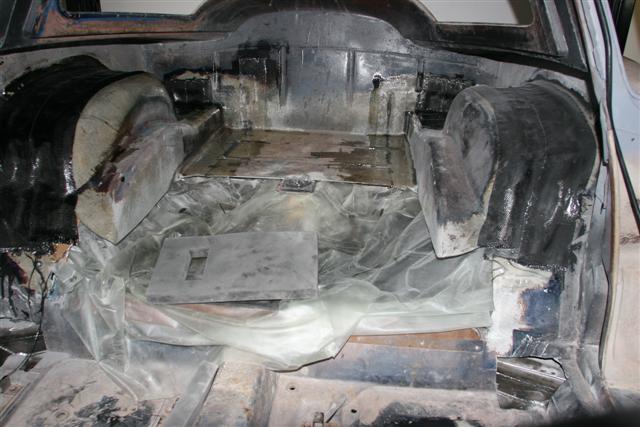