firstgear
Well-known member
- Joined
- Oct 11, 2003
- Messages
- 1,895
- Location
- Norwalk, Ohio
- Corvette
- 15 Z06, 01 Vert, 63 SWC & 60 ALL RED
Got the motor back in the frame so that I can get the new motor mounts welded onto the frame and while I was at it, I thought I would put the headers on to see how everything fits....
First problem, where the header passes underneath the oil filter it is so close that the filter can never come off...it is actually touching the end of the header. QUESTION: Is there a shorter filter than the one I have on the motor that would give me perhaps an inch more clearance? or any other kind of solution someone might have....
I don't have the starter on the motor, but I am wondering if anybody sees any other potential areas of interference....do you think the starter will be touching anything? Anything else doesn't look right?
I would appreciate comments....thanks!!!
First problem, where the header passes underneath the oil filter it is so close that the filter can never come off...it is actually touching the end of the header. QUESTION: Is there a shorter filter than the one I have on the motor that would give me perhaps an inch more clearance? or any other kind of solution someone might have....


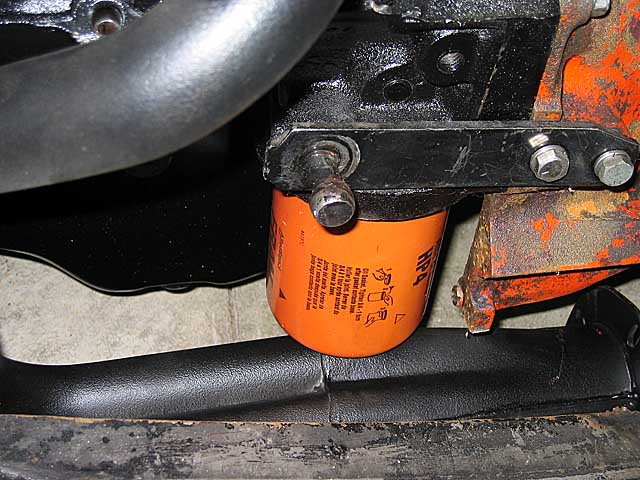
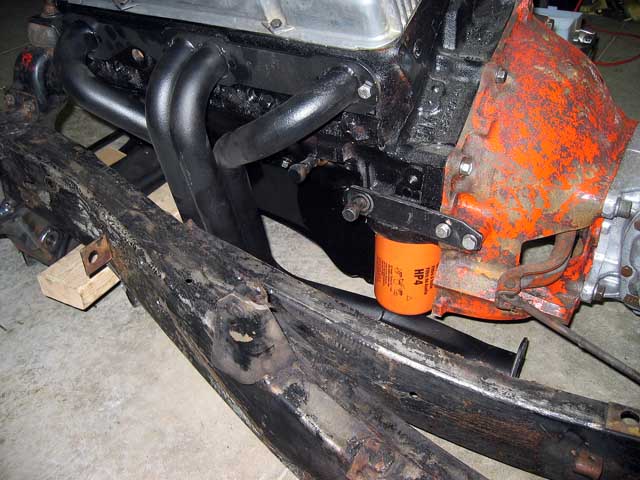
I don't have the starter on the motor, but I am wondering if anybody sees any other potential areas of interference....do you think the starter will be touching anything? Anything else doesn't look right?

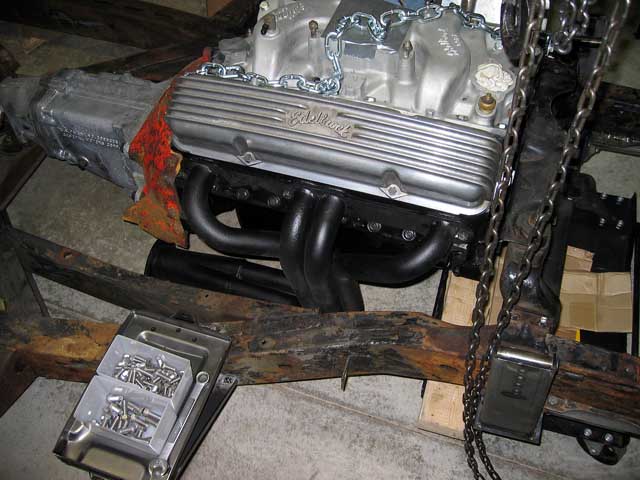
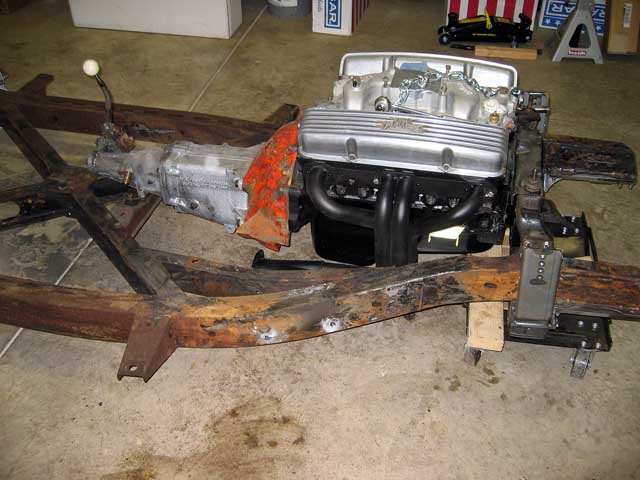
I would appreciate comments....thanks!!!