And then something else.
For some time I was thinking to get another engine. Not just to buy a compleetly new engine but to calculate everything myself, buy all the parts and assemble it myself. I'm not in a hurry but it should be in my car within 4 years (as the body off took almost 10 years I think this is doable)
First I was thinking to build a 383. As a friend had a nice 350 roller engine for sale with a 1 piece RMS I bought that one. (previous picture) But as I was searching ebay for some head studs I came across a nice Dart SHP 400ci engine. I already knew that the Dart engine really was THE engine for me but as they aren't that cheap (I have to get it to this side of the atlantic) I never gave it much thought. But this engine had less then a hour time on it as it was checked for leaks and then boxes away. As they order was cancelled they parted out the engine and put everything on ebay. Lucky for me I was the highest bidder and also for some other stuff he was selling. After some good and quick emails back and forward I transferred the money and the enige was packed for the harbor. And now (I think a month later) I have it in my garage
Yes it was a nice day when the truckdriver called me that he had arrived. As I was working my father unloaded the package and I wend looking that same evening.
Well the engine really looks great, you can still see the cross markings in the cilinderwalls and it even has the white cam grease on the cam bearings, like new but with all the engine work already done!
Here the ARP head studs I was looking for in the first place and at the back a surprise from Michael (the seller) a Cloyes timing set!
And a ATI super damper. No more problems with the original rubber line in between the damper. It also accepts a blowergear in front of it but I'll just use it like this.
And the list goes on! A flywheel also almost brand new. Don't know how many teeth but as I also need a high torque starter that isn't a problem.
Also included a set with hellfire piston rings, they were in the engine when i ran but they are all nicely labeled with the correct cilinder number. So if I may say so, his is a damn good start!
And still not all. Last week I found a nice Milodon 31506 oil pan on ebay (still in plastic) but as I was the only one bidding I got it for $150
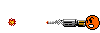
otfl The seller also included a Milodon 18465 pickup with 3/4 inlet. These parts are at this moment in a warehouse in Paramount waiting on my other parts.
I was looking for a good oil pump. Don't want no high volume or high pressure and with the 3/4 pickup inlet my choise is the Melling 10554. As I don't know how old the current water pump is I'm also going to order a new one for this engine the Milodon 16215. Those parts will be the next package crossing the ocean.
On the engine. I want it to be a torque engine as I'm not really a high rev somebody, but from time to time I still want to be able to hit 6000 rpm. As I see it now static compression will be around 9.75:1 (with iron heads and regular gas) and dynamic at 8.2:1 (thats about max I can give it when I build it myself.
The crankshaft will be a Callies Compstar, pushrods and pistons I don't know but forged steel and forged alu.
Cam and lifters Compcams (OEM roller) or something better (any suggestions?)
Heads, at this moment I have Dart Iron Eagles 180cc with 72cc combustion laying around but maybe a alu CNC head will be better for this engine. Still need to lookup the flow numbers are low lift.
Intake will be stock L81 (maybe the runners matched to the heads) or something better but I don't think there is much that will fit.
Carb will be the E4ME with some tweaks.
Exhaust already is a 2,5" true dual with x-pipe and original short tube headers. I think I'm going to change the headers in to long tubes for Stainless works. I have the time so at this moment ebay's automatic search is my friend.
What TQ and HP numbers am I looking for? Don't really care the only thing that I need is an engine so my 81 will leave my friends 86 vette far far behind!
That's it for now!
Greetings Peter